This project was made during a course about if and how everyday products can be designed in a more sustainable way.
By designing products from materials that develop an appealing patina and character during their use, an emotional attachment to the product can arise. Experiences and memories with the product combined with the patina and character can be the emotional attachment that makes the user not want to discard the product in the first place. This increases the likelihood that the product will have an extended lifespan, which benefits sustainable development.
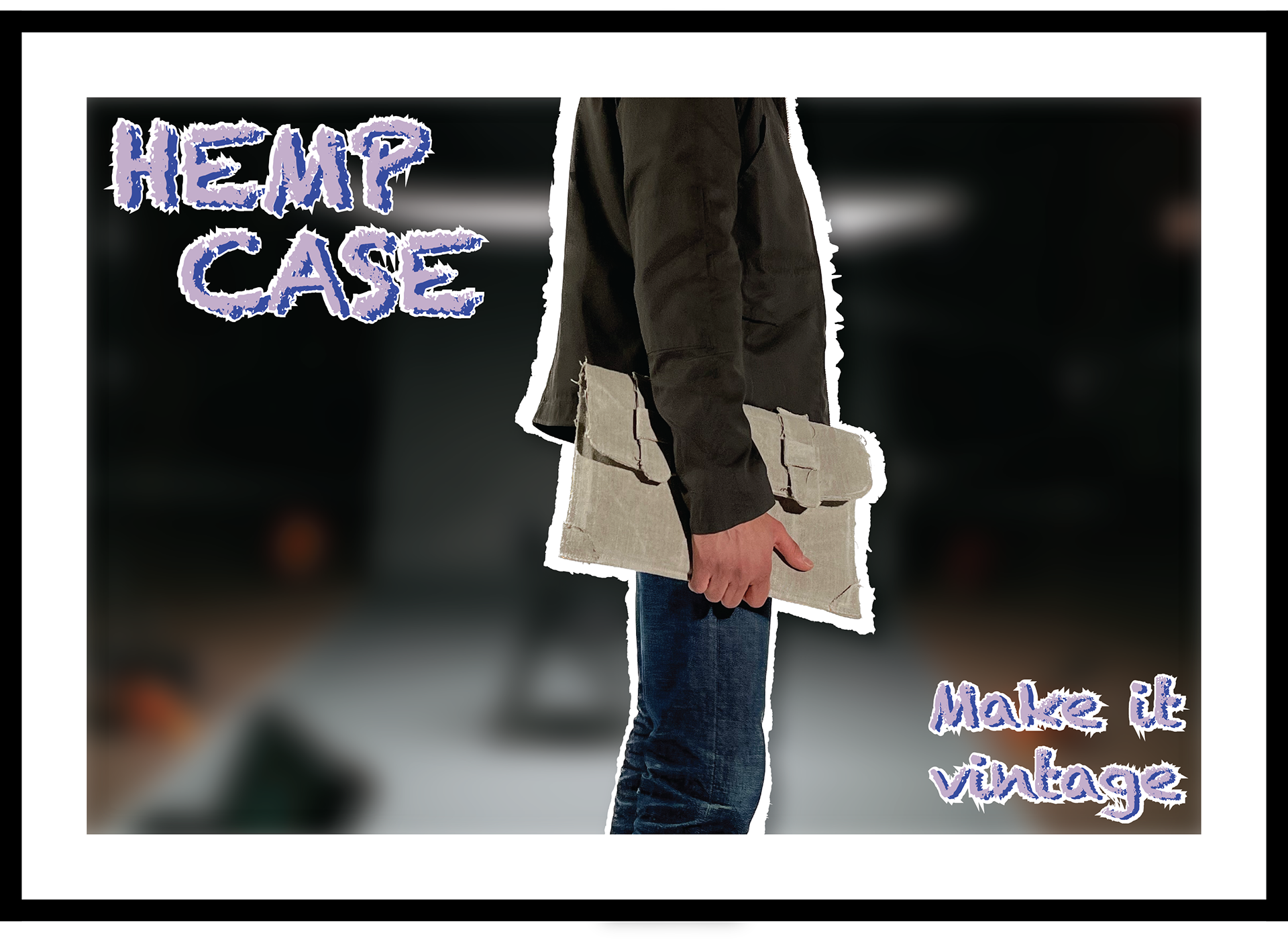
Ideation process through sketching
Prototyping process
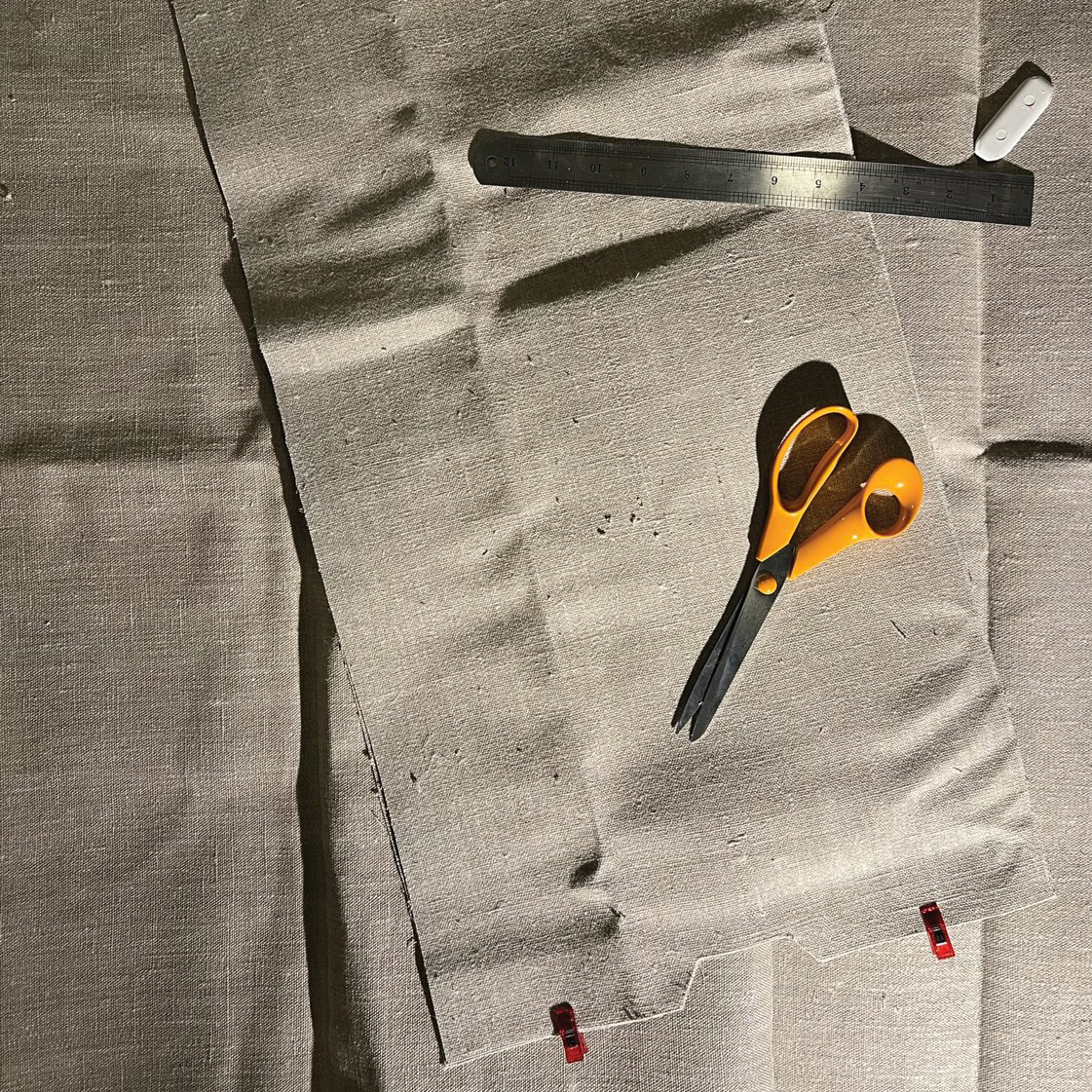
18 oz Hemp canvas fabric
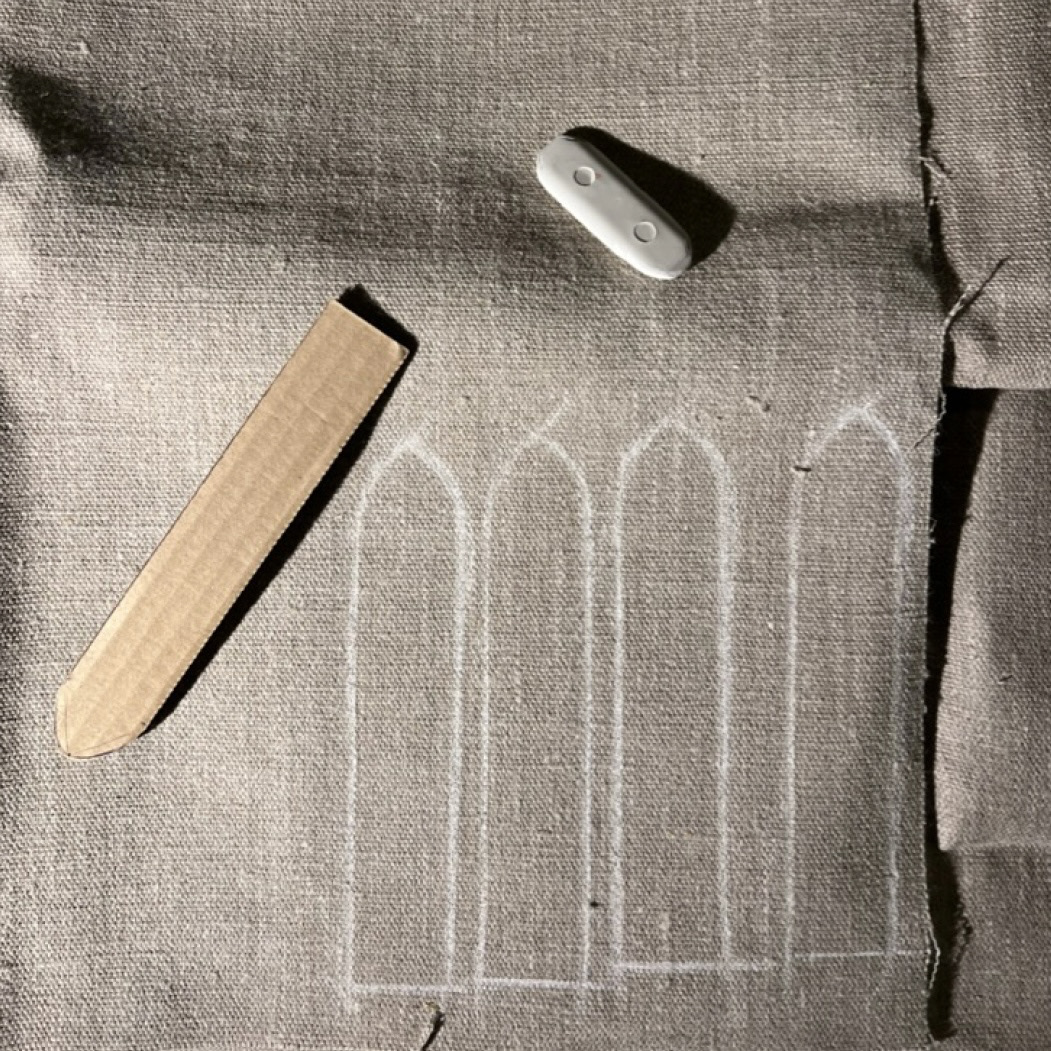
Straps
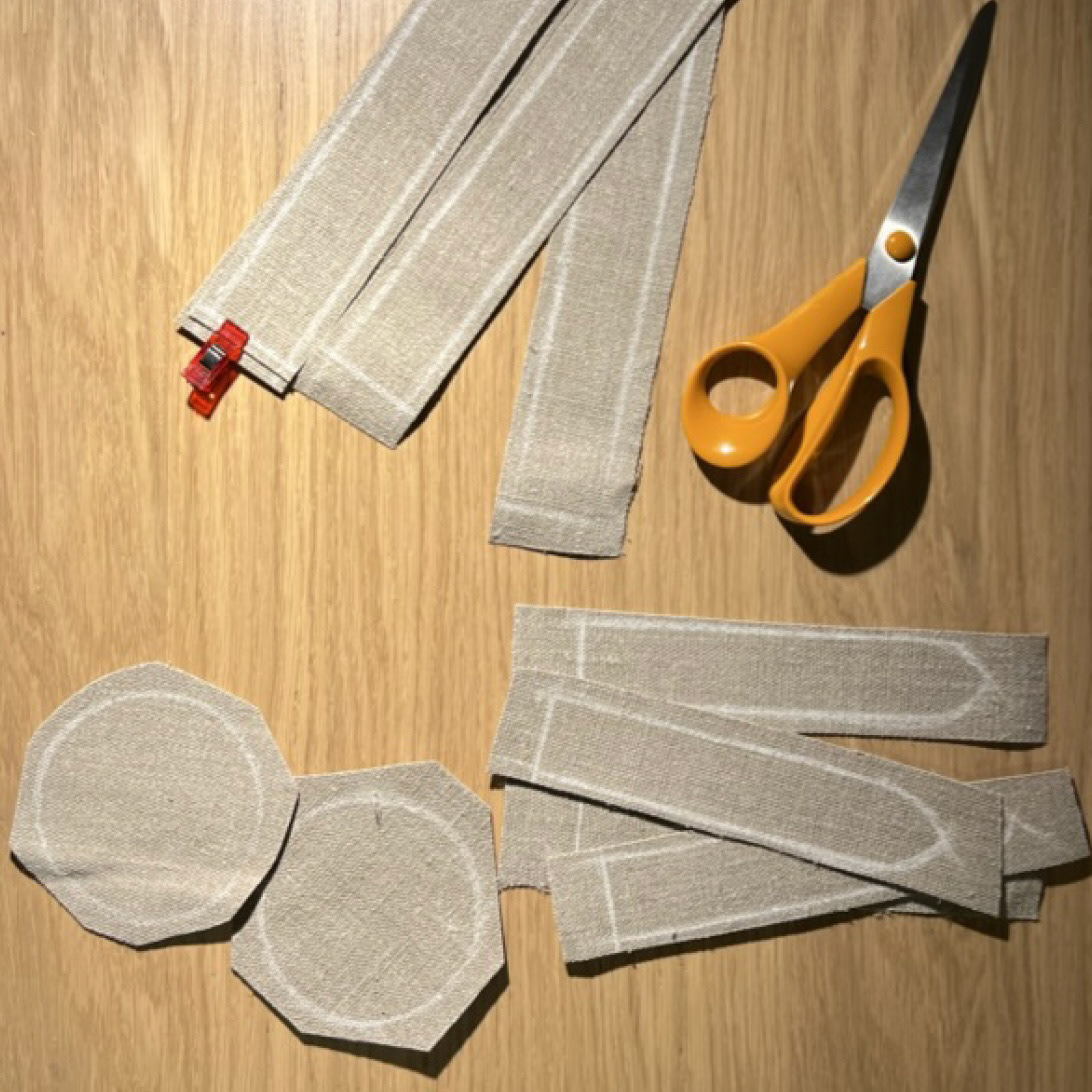
Straps, loop and corner reinforcement
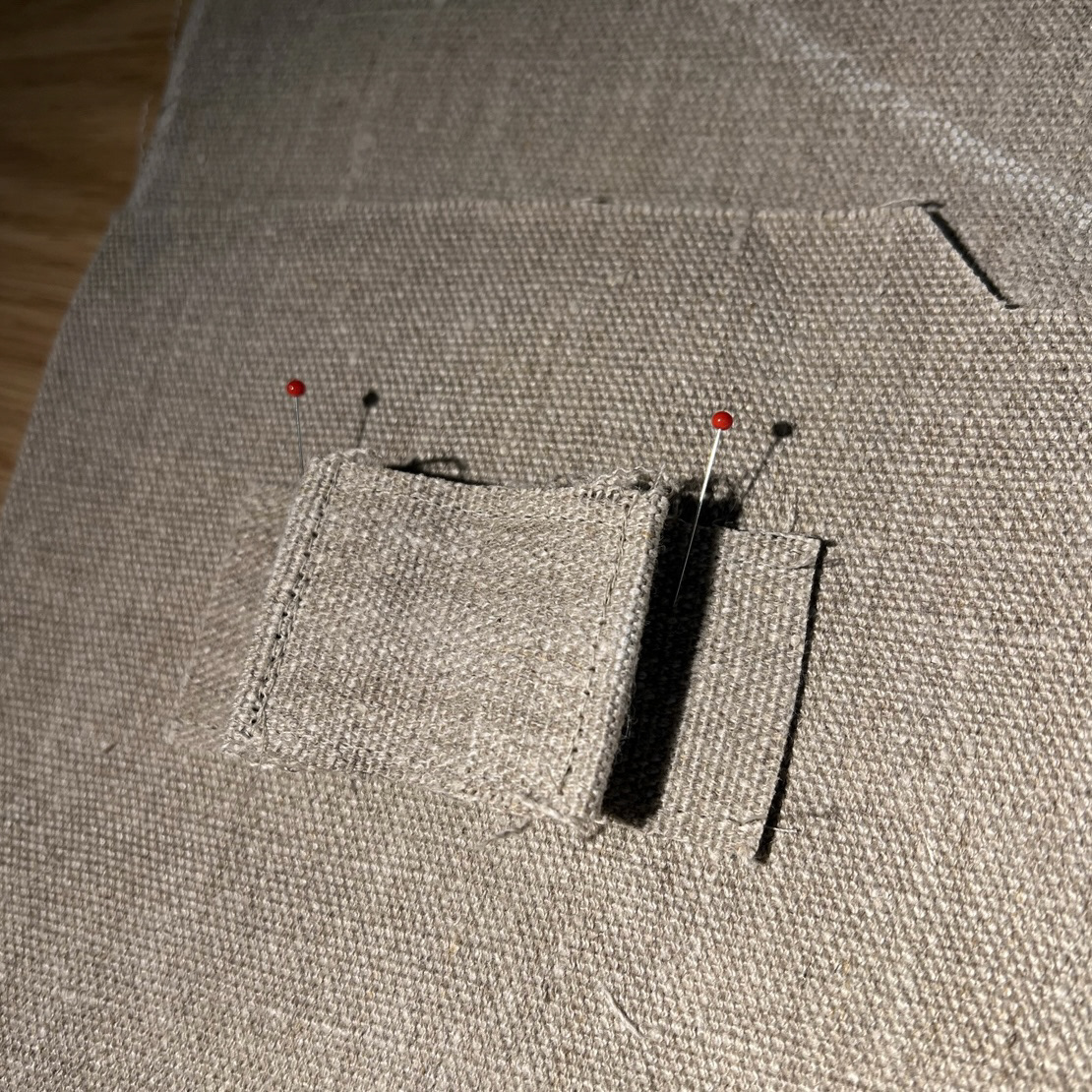
Sewing on the loops
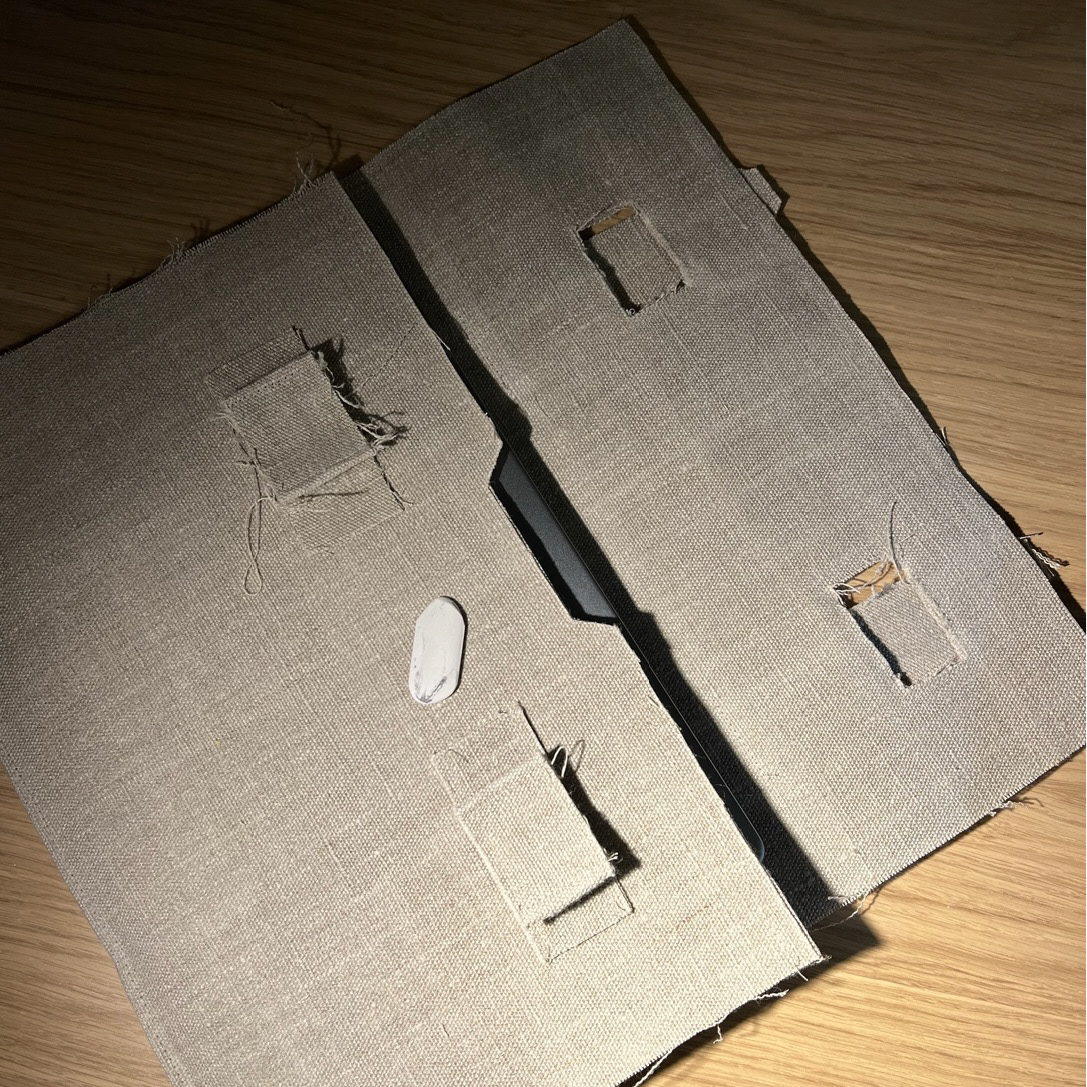
Adjustments for the final sewing
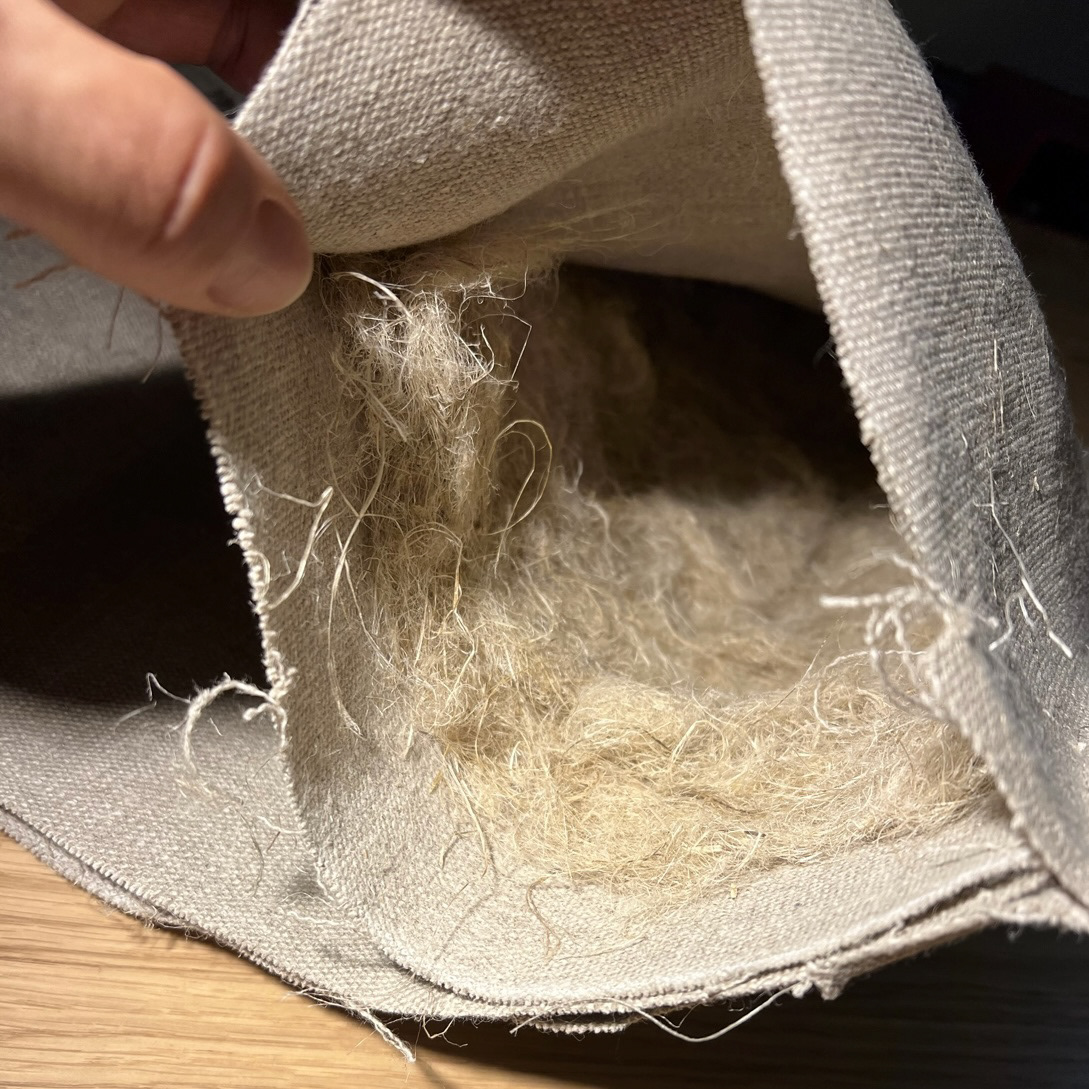
Filled with hemp padding for shock resistance
Close up pictures of unused Hempcase prototype
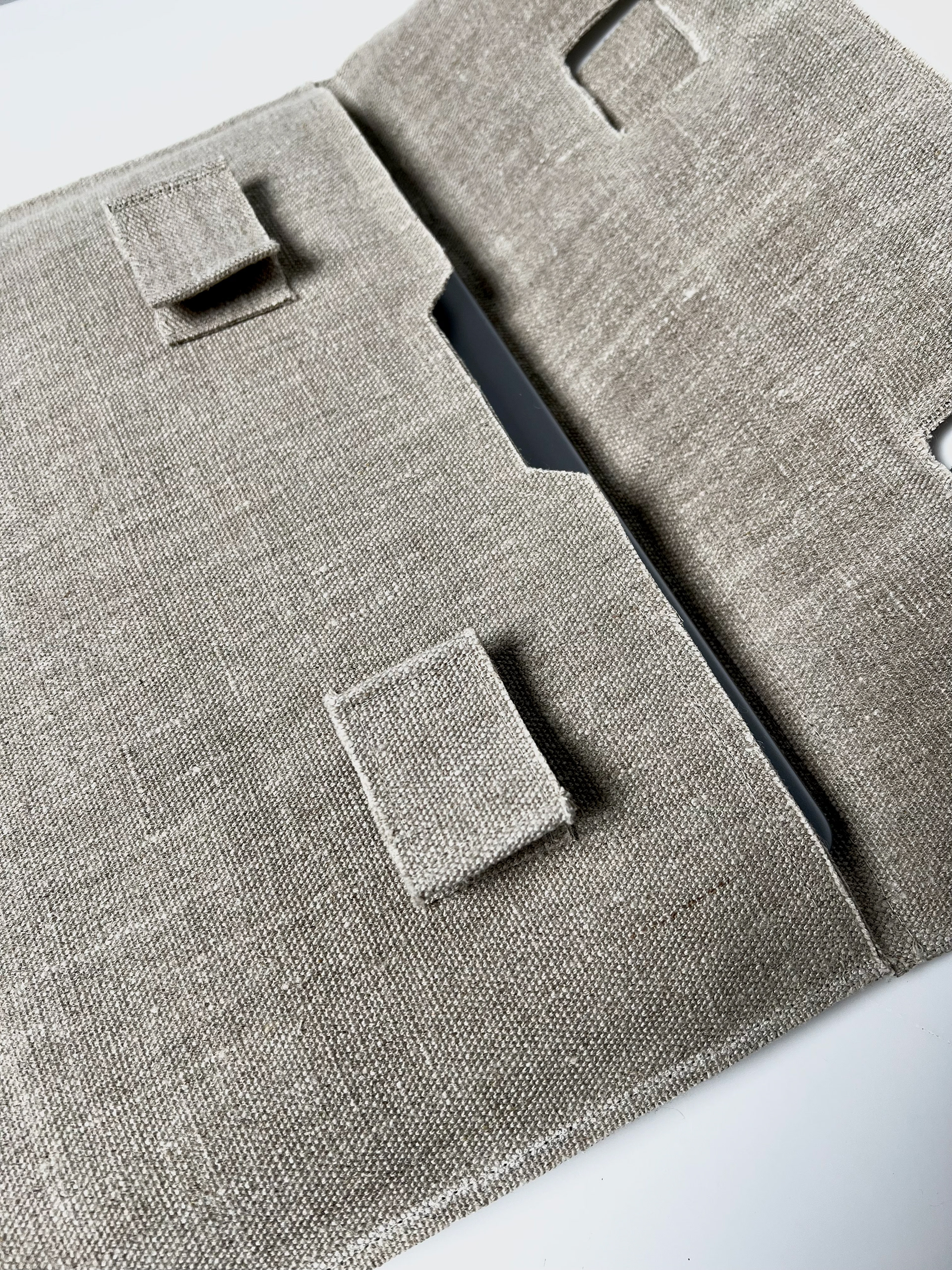
Reliable strap loops
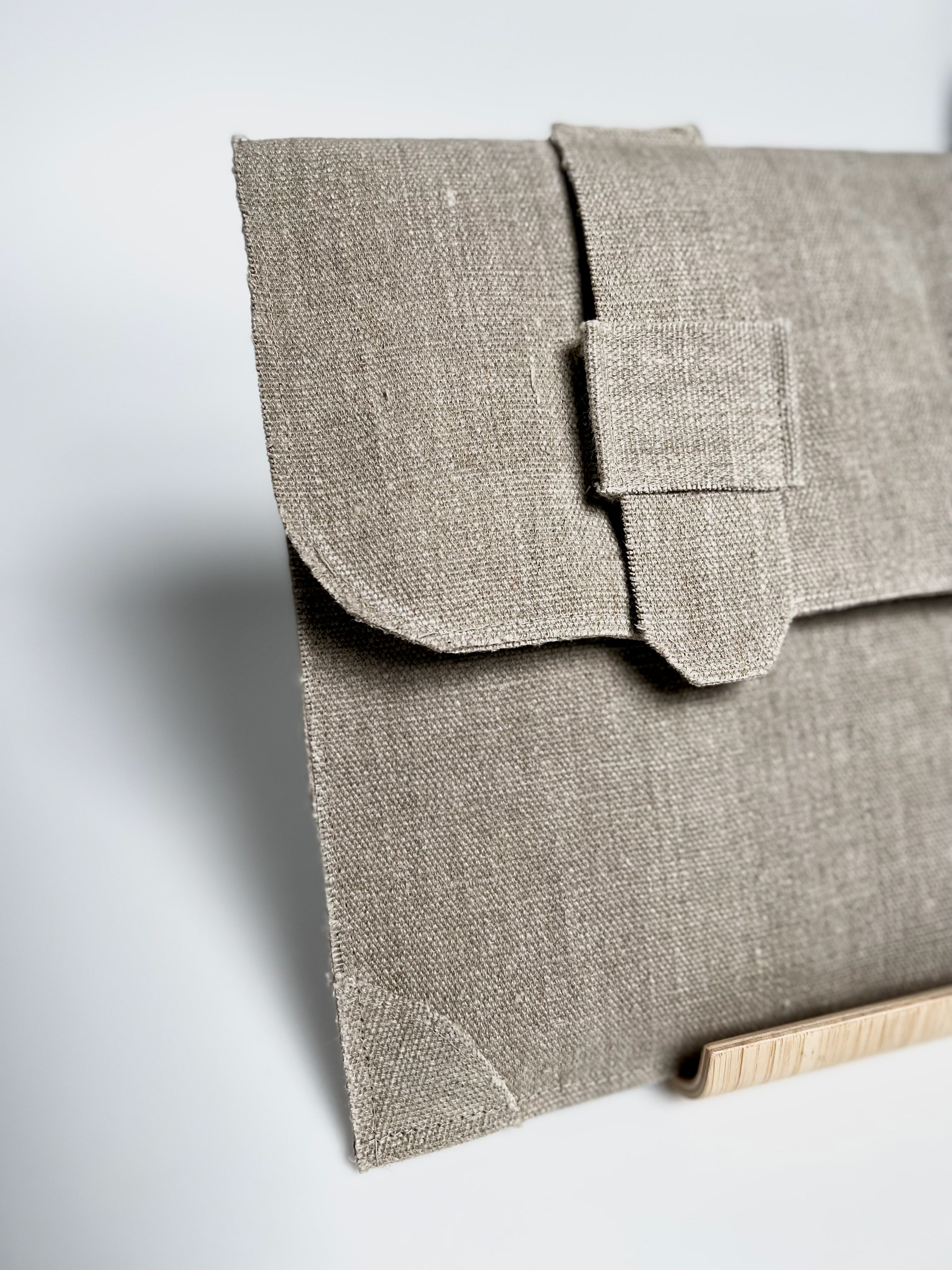
Reinforced corners
Illustration of the products journey through the biological loop based on circular economy
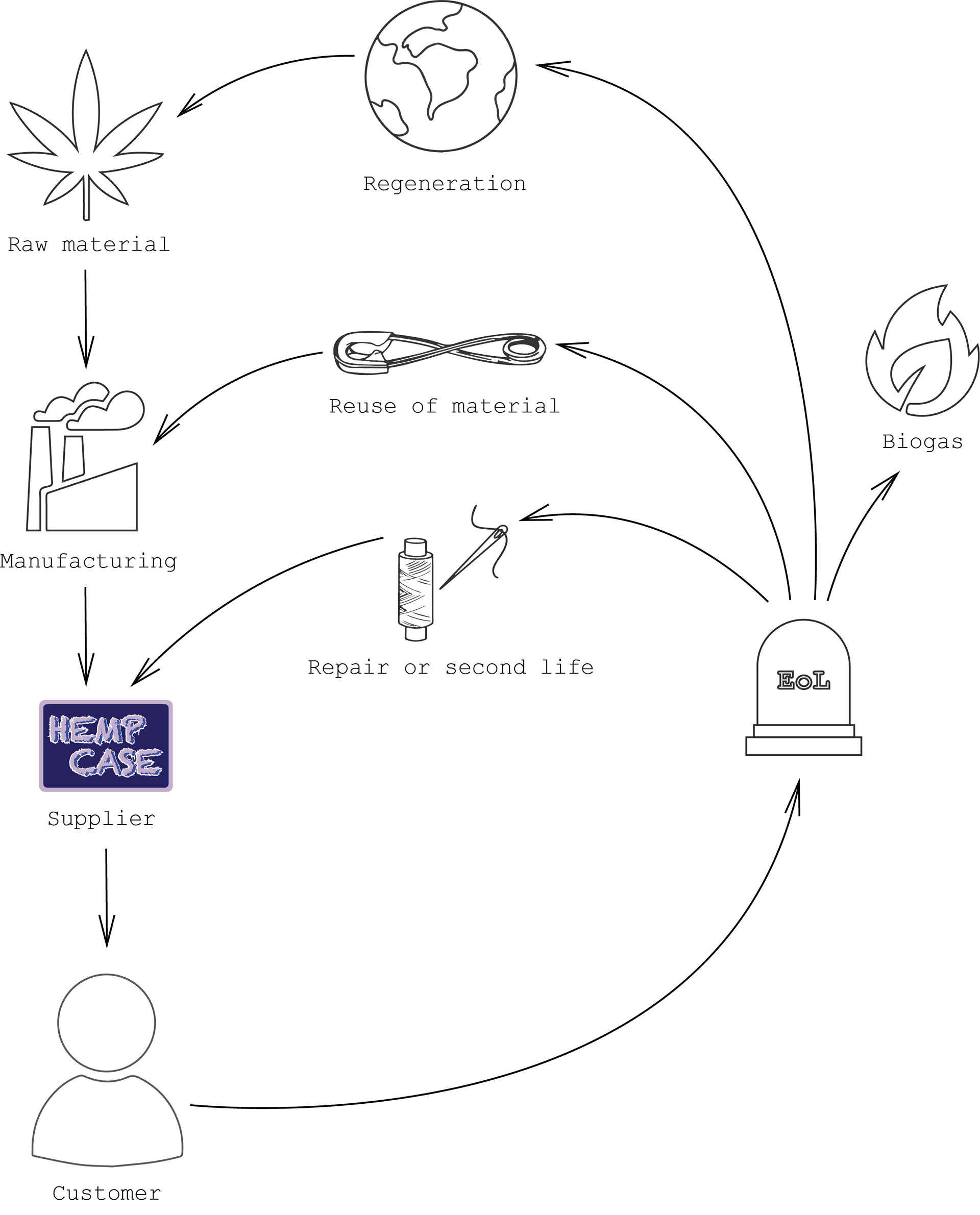
The product can be handed in to the fictitious company Hempcase for repair or as a pledge in exchange for a discount. The pledged product will be refurbished and sold as a pre-loved Hempcase to users who appreciate second-hand trade. If the product is too worn, the material will be ground down into fibers that will be used as padding in new Hempcase products.
If this closed cycle were to be broken the product can also undergo biological degradation. In this process biogas can be extracted to be used as fuel or energy. The product can also be composted and reunited with the soil which returns value in the form of fertilizer for new plants.
A representation of Hempcase potential of acquiring an attractive patina through daily use
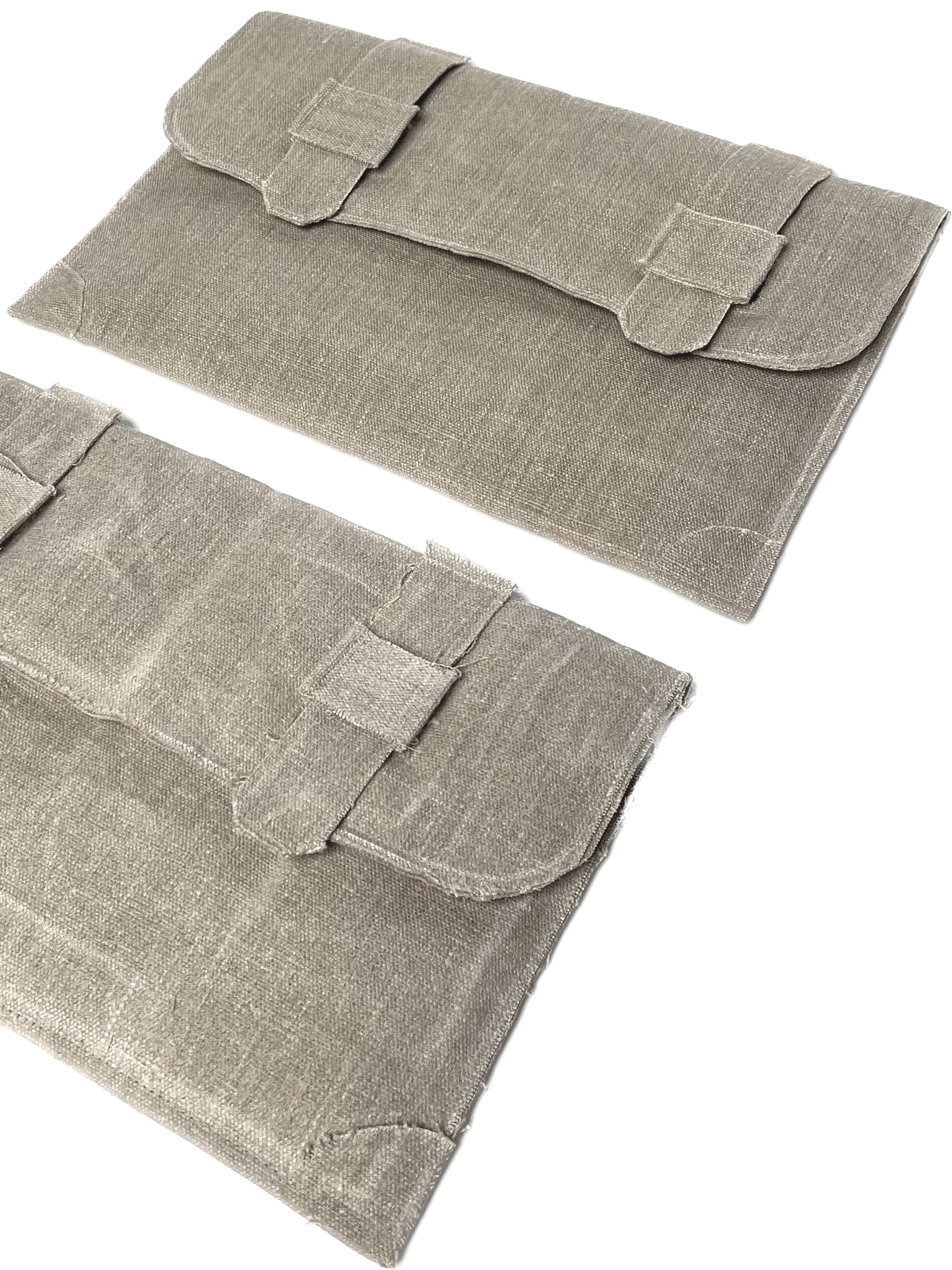
LCA
Life cycle analysis calculated with EduPack to establish how big the difference is between the energy required to manufacture the products and how much carbon dioxide that is realsed during the entire process.
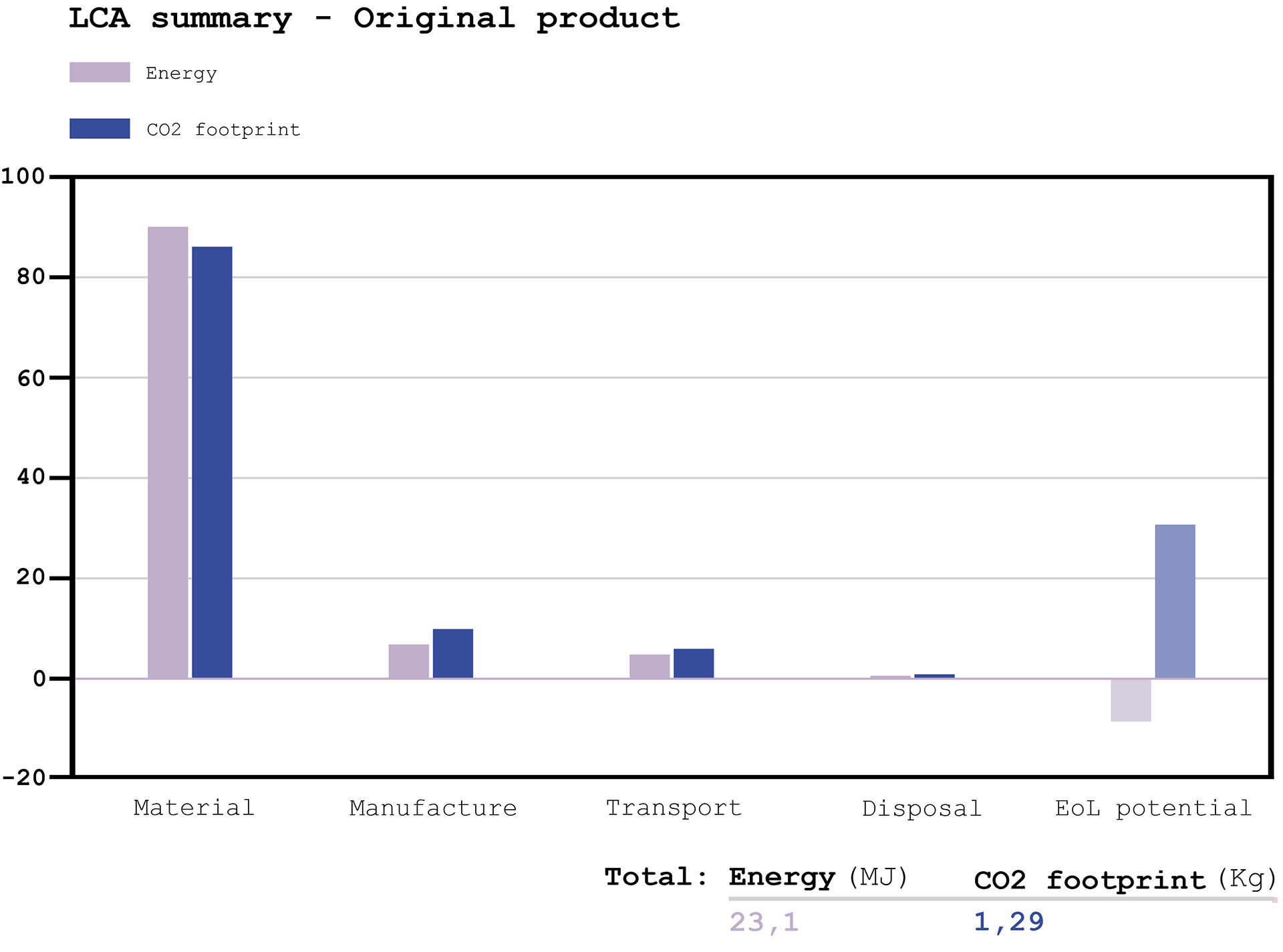
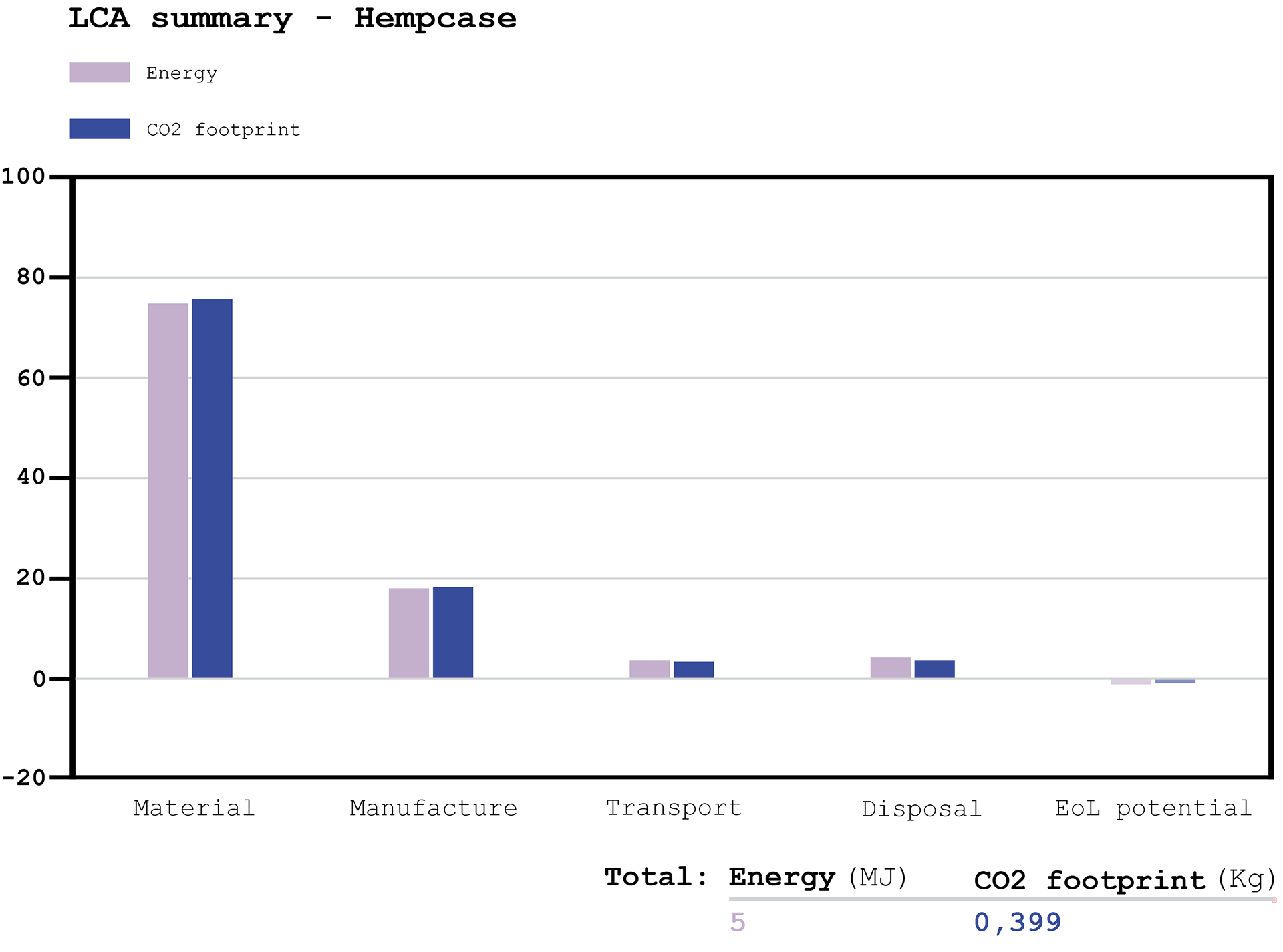
Original laptop case
The original laptop case was made up of five different materials from across the world in comparison to Hempcase that is only made from on, this enables easier recycling and a larger opportunity for the materials value to be utilised in a higher degree at the products EOL (End-of-life).
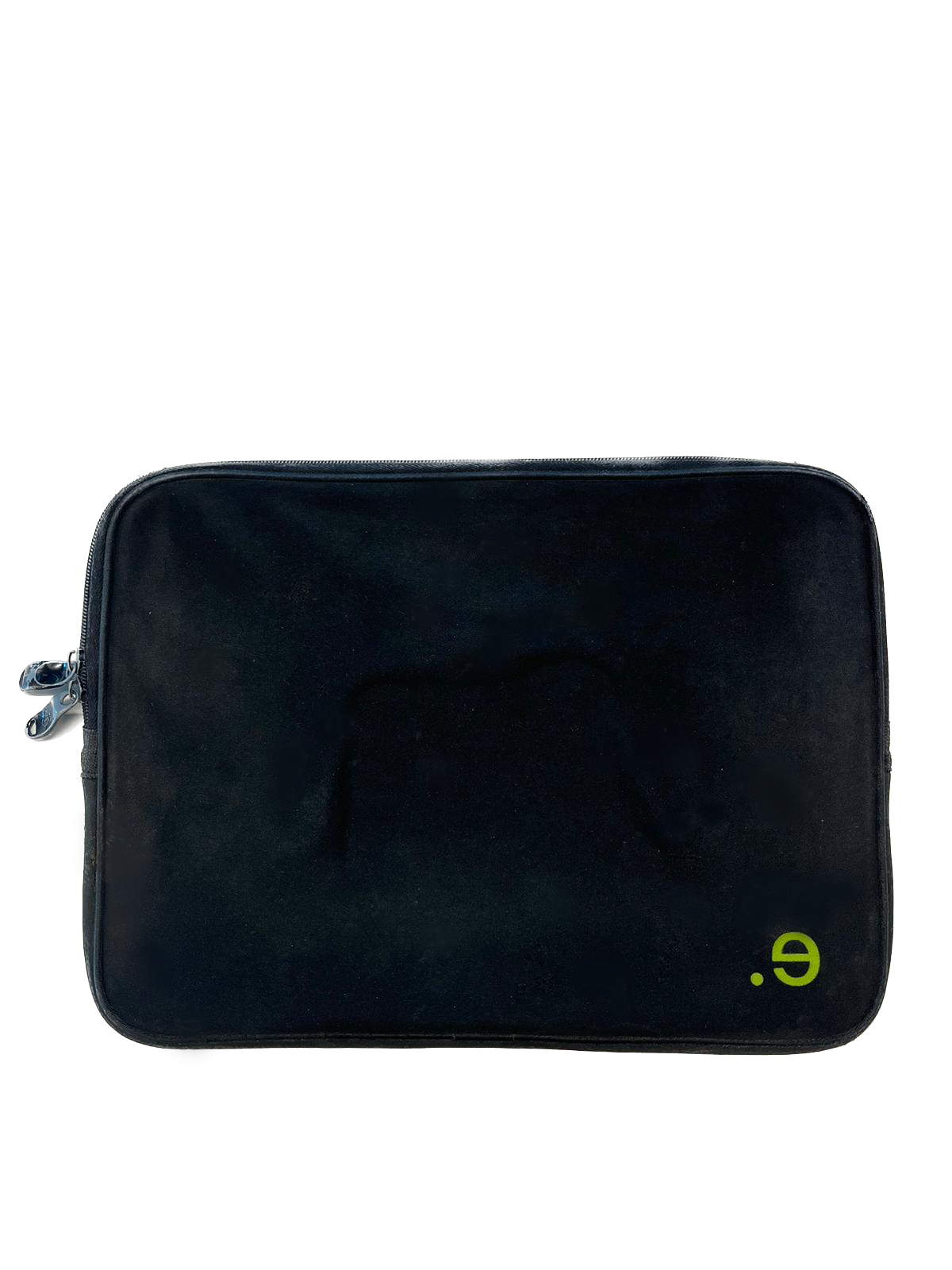
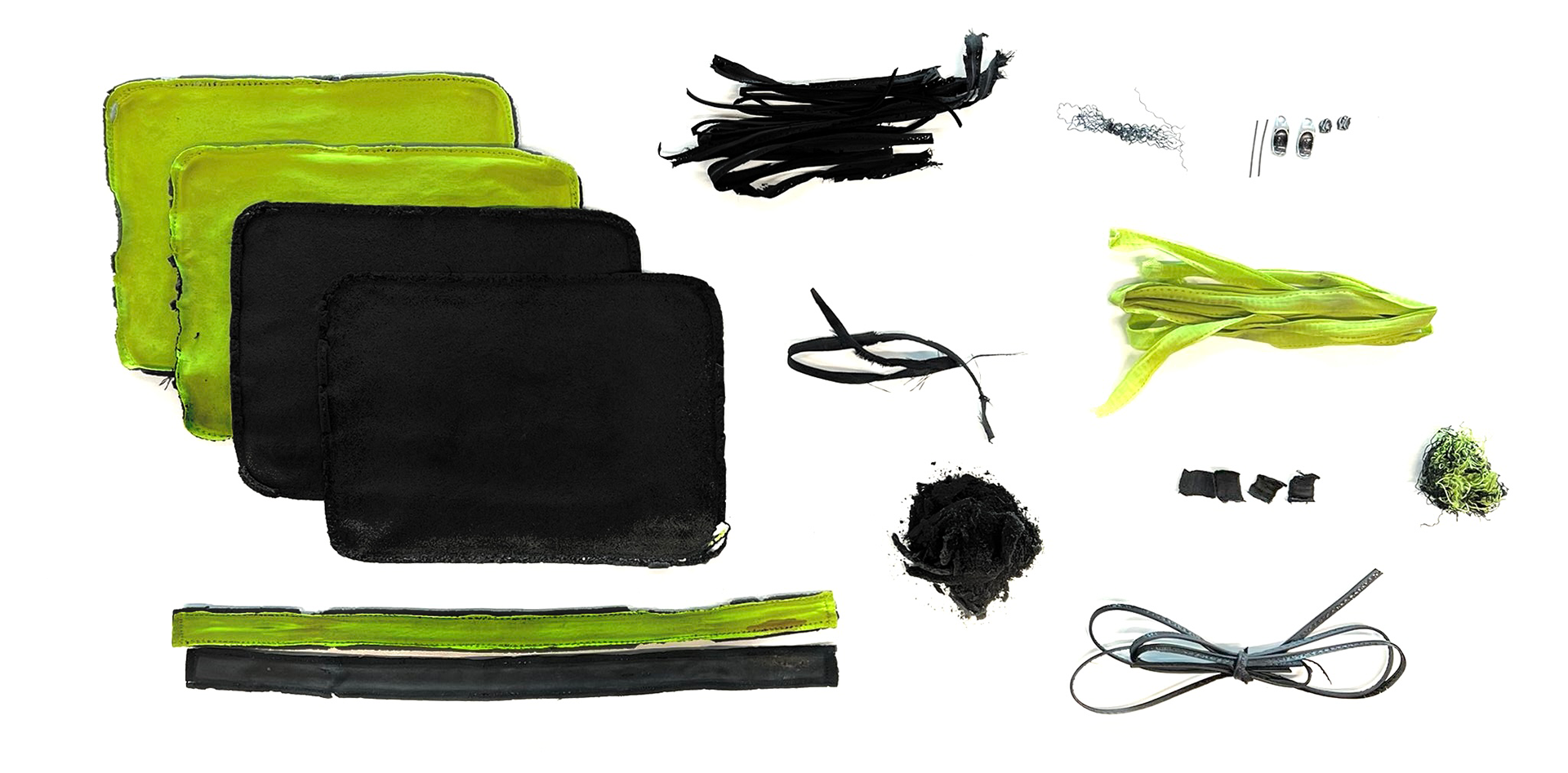